How Vaionic's modular Electric Drive Unit boosts flexibility and cost-effectiveness across use cases
- Michelle
- Nov 10, 2022
- 4 min read
Updated: Feb 7, 2023
The need for sustainable mobility solutions has birthed electric drive units or electronic power trains. The real challenge of finding an alternative due to environmental damage from fossil fuel overuse has led to innovations in the field of electrification of mass mobility. However, the development and deployment of these solutions are neither happening fast nor efficient enough. This is where Vaionic is enabling the new automotive revolution: by providing the most efficient electric drivetrain systems.
The current situation with electric drive units
Electric vehicle development teams are facing pertinent technical and commercial challenges, including high development costs, the time required for R&D and testing, expensive components, thermal limitations, and scalability. Multiple global teams are looking to address the many challenges in the development of electric drive units. Considering these challenges, Vaionic has done some truly ground-breaking work to set new standards.
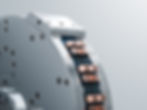
The current modular skateboard architecture relies on motors of different types and sizes to vary power classes, making the entire process cost-intensive, uneconomical, and environmentally unfriendly, usually resulting in the over- or under-powering of certain car models. Vaionic, on the other hand, has developed a drivetrain system that provides full flexibility with regard to power output, applicability, and packaging and yet, generates no additional costs for R&D, qualification, and production lines. To our mind, this is the very definition of efficient. How modularity solves these problems
The modularity of our powertrain system stems from the axial flux motor design of our motor. This topology allows us to develop our concept of modularity.
While the axial flux design is not new, it has received renewed interest in the last two decades. The use of the axial flux design (as compared to radial flux motor design) has many benefits such as achieving a higher weight-to-torque ratio, reducing core losses, achieving efficient cooling for greater stator life, achieving the lowest copper losses and the highest copper fill factor.
Full Flexibility: Power Output
Industry-standard usually defines modularity as connecting multiple motors of the same type which are combined to work as one in a particular application. This means that the entire motor, including the bearing shield, bearing, and housing, are obstructed multiple times.
Instead of duplicating the entire motor, we have to add in rotors and stators only.

Full Flexibility: Application
The modularity principle we follow in our electric drive unit design offers the perfect solution for a variety of use cases. Our e-motor’s modular design allows for variable power output modification, making it a high-efficiency unit that is relatively lightweight and volumetrically efficient. That given, it allows us to scale vertically or horizontally.
The principle of modularity in our motors also enables quick and efficient solutions to reduce emissions. For instance, a passenger bus with reduced motor volume can be designed to carry a higher number of passengers. This will lead to a reduced number of buses and trips and subsequent savings in costs and lower CO2 emissions. The reduced motor weight in commercial vehicles leads to an increased amount of freight per vehicle, leading to fewer trips and savings.
Full Flexibility: Packaging
In comparison to current machines, our e-motor designed following our unique concept of modularity produces a power-to-magnet-mass ratio that is four times greater than comparable motors. Yet, this design is up to 93% more compact while providing the same power output compared to conventional e-motors and utilizing up to 90% less resources at equal power output. Our motors use around 90% less copper, and the ease of disassembly and retrieving of magnets helps in reusing the rare earth elements more efficiently, and yet, generates no additional costs for R&D, qualification, and production lines.

Each application usually requires multiple endurance tests that are expensive and time-consuming. But since our innovative modular electric drive system is completely tested, we are able to reduce testing time and limit it to only different motor housings or plugs for all further developments. Our modular design also results in having much lower development and validation costs since a single motor concept and design can address multiple applications with different power requirements.
Since the disc-shaped parts of our system reduce the complexity of production, our production processes are much simpler than comparative electric drive system suppliers. The production focuses more on the rotor and stator, and it is only the application that eventually decides on the final assembly. The high degree of flexibility offered by our electric drive system stems from the fact that only the power requirements, i.e., the number of rotors and stators built in the system along with the slight adjustments in our power electronics, of a particular application need to be considered. Thus, we are able to react quickly and supply different power classes fast without added time of development and are able to help save millions of USD in development and operational expenses.
Parting thoughts
In a bid to keep up with the lightning-fast market, electric car manufacturers are in need of easily adaptable solutions that will help them transition seamlessly between models without having to spend immense amounts of time and money on development. To meet this objective, they need trusted partners with proven competencies who live and breathe electric drive units to help them easily integrate the powertrains into their vehicles.
The team at Vaionic is creating industry benchmarks that are sure to be followed in the years to come. By developing cost-efficient systems that support sustainability, Vaionic is setting the stage for the next phase in the electric mobility revolution.